Traditional vs. Modern Iron Smelting Furnace: What’s the Difference?
Iron smelting furnace has played a pivotal role in human history, shaping economies, industries, and technological advancements. From the basic blast furnaces of the ancient world to the cutting-edge induction furnaces of today, the evolution of iron smelting technology highlights a constant drive for efficiency, safety, and sustainability. In this blog, we explore the differences between traditional and modern iron smelting furnace, focusing on the significant improvements in technology, safety, and energy efficiency, followed by an introduction to the Intermediate Frequency Coreless Induction Furnace developed by Guangdong Rongke Industrial Equipment Co., Ltd.
The Basics of Traditional Iron Smelting Furnace
Ancient Technology: The Blast Furnace
Traditional iron smelting furnaces, particularly the blast furnace, date back to the early civilizations. They relied on natural draft or forced air, usually delivered by bellows, to heat iron ore in the presence of carbon, typically in the form of charcoal. The goal was to reach temperatures high enough to reduce iron oxide (ore) to produce molten iron.
These early furnaces were massive, labor-intensive structures that could take days or weeks to operate. The fuel efficiency was low, requiring large quantities of wood and charcoal, leading to deforestation in some areas. Nonetheless, this technology enabled the mass production of iron, helping forge tools, weapons, and infrastructure.
Fuel and Temperature Control
One key characteristic of traditional furnaces is their limited ability to precisely control temperature. The use of coal or charcoal as the primary fuel source made it difficult to achieve consistent temperatures. The inconsistent heating often resulted in varying quality of the iron produced, affecting the final product’s strength and durability.
Environmental and Labor Impact
Traditional iron smelting furnaces were not only inefficient in terms of energy consumption but also harmful to the environment. Large amounts of carbon emissions, coupled with the deforestation caused by the heavy reliance on charcoal, created a substantial environmental footprint. Additionally, the physical labor involved in operating these furnaces was immense, with workers exposed to high temperatures and hazardous conditions.
Modern Iron Smelting Furnace: Efficiency and Precision
Technological Advancements in Modern Furnaces
Modern iron smelting furnaces, such as the Intermediate Frequency Coreless Induction Furnace, represent a leap forward in terms of efficiency, safety, and environmental impact. These furnaces use electrical energy to create an electromagnetic field, which heats the iron ore or scrap metal inside the furnace. This method allows for precise control of temperatures, significantly improving the quality and consistency of the molten iron.
Moreover, modern furnaces are much faster in production cycles compared to traditional blast furnaces. What took days in a traditional furnace can now be achieved within hours, allowing for continuous, uninterrupted production. This efficiency not only increases output but also reduces energy consumption, making the process more sustainable.
Energy Efficiency and Reduced Emissions
One of the standout features of modern smelting furnace is its energy efficiency. The use of electrical induction technology drastically reduces the amount of fuel required to reach the necessary smelting temperatures. This not only reduces operational costs but also minimizes carbon emissions, contributing to a lower environmental footprint.
Additionally, modern furnaces are designed with energy-saving technologies, such as improved insulation and heat recovery systems, further enhancing their energy efficiency. This contrasts sharply with traditional furnaces, where much of the heat generated is lost to the environment, leading to inefficiency.
Enhanced Safety Features
Modern iron smelting furnace prioritizes worker safety. Furnaces like the Intermediate Frequency Coreless Induction Furnace are equipped with advanced safety systems that monitor furnace conditions in real time. Leakage alarms and grounding alarm systems are in place to ensure that any breach in the furnace lining is detected immediately, preventing potentially catastrophic accidents.
In contrast, traditional furnaces offered minimal safety features. Workers were often exposed to high levels of heat, harmful fumes, and molten metal, increasing the risk of injury or fatality. The shift to modern technology has vastly improved the working conditions in iron smelting facilities.
Introduction to the Intermediate Frequency Coreless Induction Furnace
A Revolution in Iron Smelting Technology
The Intermediate Frequency Coreless Induction Furnace from Guangdong Rongke Industrial Equipment Co., Ltd. represents the pinnacle of modern smelting technology. This furnace integrates cutting-edge materials and processing techniques, ensuring superior performance in terms of safety, stability, and energy efficiency.
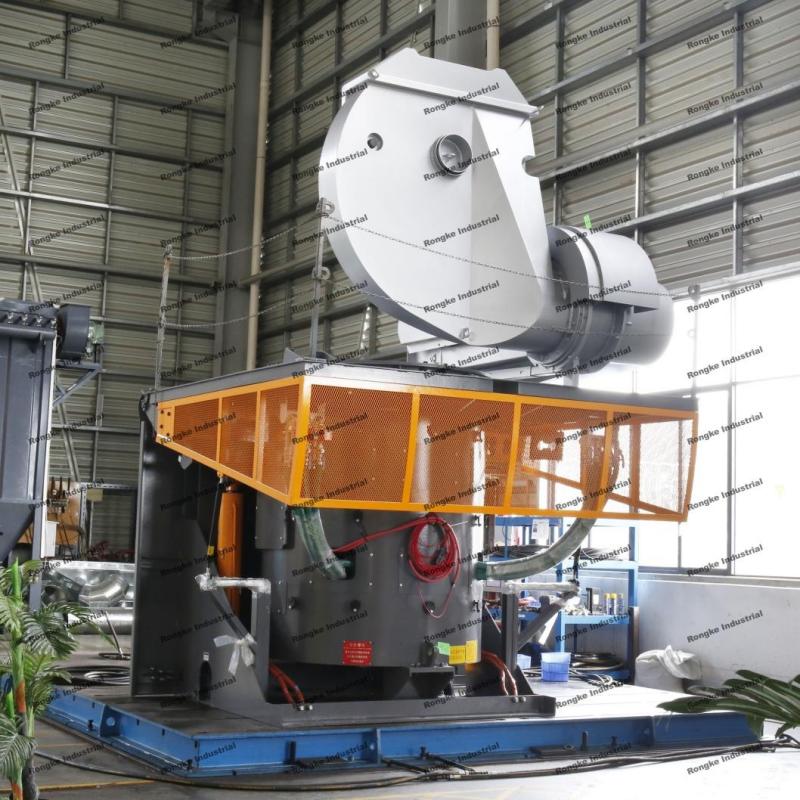
The furnace body features interactive windows and quality details, offering operators real-time insights into the smelting process. This combination of technology and craftsmanship positions the furnace as a leader in the industry. Its innovative design allows for safer, more reliable production, making it an ideal solution for modern iron smelting needs.
Advanced Safety Systems for Reliable Operation
One of the most important aspects of the Intermediate Frequency Coreless Induction Furnace is its state-of-the-art safety system. The Rongke IDE full-time and all-around furnace leakage alarm system is a patented design certified by the EU CE safety system. It utilizes a two-level detection principle to monitor the integrity of the furnace lining and coil.
When molten iron seeps through the furnace lining, the leakage current alarm is triggered as soon as the iron comes into contact with the detection electrode. If the iron penetrates further and reaches the coil, a voltage detection circuit is activated, indicating the specific location of the breach. Additionally, a grounding alarm detection system monitors the proximity of molten iron to the coil, providing multiple layers of protection to prevent accidents.
Leading Energy Efficiency and Durable Construction
The Intermediate Frequency Coreless Induction Furnace is built with energy efficiency at its core. The furnace coil, made from TU1-grade oxygen-free copper provided by Chinalco Luoyang Copper Co., Ltd., uses a thick-walled copper tube produced via cold extrusion. This high-quality material, combined with the double coil technology, ensures the furnace operates with maximum energy efficiency.
Another key innovation is the use of magnet yoke technology. The yoke is made of high-quality cold-rolled oriented silicon steel sheet. It minimizes magnetic losses and ensures better energy transfer to the molten pool. With a coverage rate of over 70%, the yoke has high heat dissipation efficiency, which can support both the induction coil and heat management. Extend the working life of the furnace while minimizing energy consumption.
Why Choose Guangdong Rongke Industrial Equipment Co., Ltd.?
Pioneers in Furnace Technology
Founded in 2013, Guangdong Rongke Industrial Equipment Co., Ltd. has become a leader in the iron smelting industry. The company was the first in the industry to achieve EU CE certification and ISO quality management system certification, reflecting its commitment to quality and safety. With significant investment in research and development, Rongke continues to innovate, delivering energy-efficient and reliable smelting solutions.
Industry Recognition and Expertise
The company’s reputation is backed by numerous awards, including the titles of “Quality, Service and Reputation AAA Enterprise” and “Low-Carbon Environmental Protection and Energy-saving Innovation Brand.” These accolades underscore Rongke’s dedication to sustainability, safety, and excellence in furnace manufacturing.
A Professional Team at the Forefront
Guangdong Rongke’s success is also driven by its team of highly skilled engineers and operators. The team brings extensive experience in operating medium-frequency induction furnaces, from raw material preparation to fine-tuning production. This deep expertise ensures that every furnace performs at its peak, delivering reliable and consistent results for customers.
Conclusion
The shift from traditional to modern iron smelting furnaces reflects significant advancements in technology, safety, and energy efficiency. Modern furnaces like the Intermediate Frequency Coreless Induction Furnace offer a safer, more efficient, and environmentally friendly solution to iron smelting. With Guangdong Rongke Industrial Equipment Co., Ltd. at the forefront of furnace innovation, businesses can expect cutting-edge technology that meets today’s industrial demands while preparing for a sustainable future.